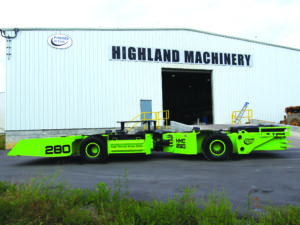
With a certified four-point canopy, the Model 280 is 34 ft long and 9 ft wide, with ground clearance of as much as 15 in. (Photo: Highland Machinery Corp.)
Highland Machinery Corp. and Grace Equipment Co. each have a superior solution for those looking to buy new and those looking to rebuild
by jesse morton, technical writer
Having a scoop rebuilt can save money over buying new, but it is still an expense. Better is needing neither, which is the case for owners of the Highland Machinery Corp. Model 280, the OEM said. The proven unit has benefited from numerous upgrades over the years and can now sometimes go for up to 16 years without needing a major overhaul.
For those miners in the market for a rebuild service, plan ahead, Grace Equipment said. The supplier offers fast turnaround times, but currently business is stacking up. Customers are increasingly capitalizing on the company’s ability to rebuild to like-new specifications almost any make and model.
Both companies said they have, can get, or can machine the parts needed to complete orders timely, which sets them apart these days, as does the superior work for which they are renowned.
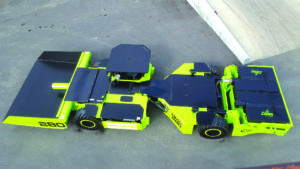
The Model 280 can be built to run on either a 128-V or a 240-V lead-acid battery, a DC or AC traction system, and a DC or AC hydraulic pump motor. (Photo: Highland Machinery Corp.)
Low-seam Scoop for Any Task
Highland Machinery Corp. said the versatile Model 280 scoop for low-seam mining can tackle “any tasks” and in most conditions. “The machine speaks for itself in its capabilities and proven performance,” said Jarrod Bailey, executive vice president.
Like the company, which has been in business more than three decades, “the 280 had humble beginnings, and started out with a lot to prove,” he said. “It has proven itself time and time again with every machine we have put into service.”
The unit’s “construction exemplifies Highland’s mission of exceeding industry standards compared to what other manufacturers offer and construct,” Bailey said.
At roughly 34 ft long and 9 ft wide, and with ground clearance of as much as 15 in., the 280, like all of Highland’s scoops, is highly customizable. A 140-ft3 bucket, a 60-gallon hydraulic oil tank, John Deere planetary four-wheel-drive axles, and a certified four-post canopy come standard. Options include a hydraulic winch, a camera system, and a proximity detection system.
“We offer a variety of attachments, which include the standard bucket with ejector blade, standard bucket with rock dust bucket, maintenance center bucket, hydraulic forklift mast, road grader attachment, and dozer blade,” Bailey said.
The unit’s top feature is the rugged frame, built and designed in house. “The frame is the most important part of any piece of equipment,” he said. “While components can be replaced and upgraded over time, the frame is the life of the machine.”
The frame contributes to the superior longevity of the 280, which can run for 16 years or more.
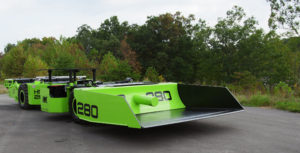
With a 140-ft3 bucket, the Model 280 features a rugged frame, built and designed in house. (Photo: Highland Machinery Corp.)
“Numbers like this speak for themselves,” Bailey said. For comparison, “our equipment rebuild shop has performed complete rebuilds on 5-year-old competitor machines that needed frame replacements.”
The scoop can be configured for either a 128-V or a 240-V lead-acid battery, a DC or AC traction system, a DC or AC hydraulic pump motor, “along with other options,” he said.
“Highland has been involved in battery development projects for the past 15-plus years with multiple battery manufacturers worldwide,” Bailey said. “We have explored multiple different chemistries and battery types.”
The scoop has a spacious and comfortable cab. “Along with options such as left-hand steering, joystick integration, diagnostic displays, and interactive information centers, the 280 allows for the operator to be comfortable while operating the machine, and to have easy access to common functions,” he said.
Over the years, updates to the model have focused on simplifying and streamlining maintenance tasks. “Zone lubrication, an automatic lubrication system, moving filtration, dedicated compartments located near the hydraulic pump, and many other improvements allow for easier maintenance,” Bailey said. “Our various electrical systems also allow for easier troubleshooting and diagnosing issues.”
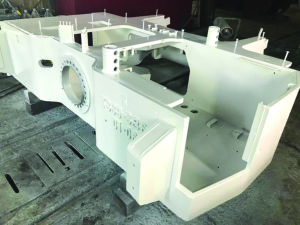
For the typical scoop rebuild, Grace Equipment Co. will tear the unit down to the frame, rebuild it from the frame up, plumb it, wire it, put lights on it, sandblast it, paint it, and send it back to the customer. (Photo: Grace Equipment Co.)
The advice received from external maintenance techs helps drive development of upgrades to the scoop. “Highland works hand-in-hand each and every day with mine maintenance departments around the world and one thing that we do is listen,” he said. “These are the people who we have to ensure are happy with the machine and who can identify areas that could need possible changes or improvements.”
Maintenance of the 280 is fully supported by the supplier. “We have a full field service division that is available 24/7 for diagnosing issues and helping to provide technical support,” Bailey said.
“Our parts division also is there to ensure that, when you do need a part for your machine, Highland will be there to provide the replacement and get you back up and running,” he said. “Our parts division has dedicated routes that are capable of servicing all Northern, Central, and Southern Appalachian mines multiple days per week.”
If the customer is new, “we can also offer additional services and support to their existing equipment with our parts division, which carries replacement parts for most all manufacturers and types of equipment, and our field service department, which works on most all brands and types of equipment to provide solutions and diagnostic services,” Bailey said.
Highland Machine Corp. offers same-day order fulfillment on motor freight, and ships with next-day-air and standard ground “to ensure your parts get to you as quickly as possible,” he said.
The first 280 was delivered more than two decades ago. “Over the course of 20 years there have been many updates made to the machine to make up the current generation of the 280 scoop,” Bailey said.
“While the original machine was a standard 128-VDC machine, standard for the time of production, the machine proved one thing for certain,” he said. “Like all machines that Highland manufactures, the machine is built to out-perform customer expectations and outlast competitor machines.”
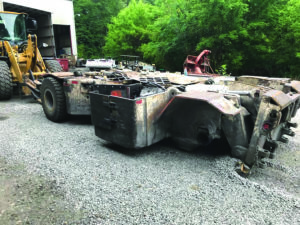
Typically the customer is responsible for transporting the scoop to Grace Equipment, that will then tear it down and assess it prior to offering options for the rebuild. (Photo: Grace Equipment Co.)
Like New at a Fraction of the Cost
Grace Equipment Co. said it is experiencing a surge in demand for rebuilds, and that it has the facilities and technicians to continue to take on new customers and keep turnaround times short.
“We stay pretty well booked,” said Frank Pearson, vice president. “We have got orders constantly coming in.”
The company rebuilds conveyors, mantrips, and other equipment, including scoops. “We rebuild a wide variety of machines,” Pearson said. “We rebuild scoops from the ground up,” he said. “We’ve got one right now getting ready to go in the shop.”
Planned correctly, a mining scoop rebuild will perform like a new machine “at a fraction of the cost,” the company said. In the typical rebuild, cylinders are rebuilt or replaced and tested. “Frame and body damage is repaired to specification.”
Hydraulic hoses and lines are replaced. “Major components are repaired or replaced,” the company said. Wire harnesses are replaced.
“We go through everything and put everything back on it new, all new hoses, all new wiring, new lights,” Pearson said. “We rebuild all the components on it that can be rebuilt,” he said. “If not then we buy new.”
The process typically starts with a phone call. “We will go take a look at it, and then figure out a time and date that we can get started on it,” Pearson said.
The customer brings it in and then “we tear it down and do an evaluation of it,” Pearson said. “Some of our customers want you to do an evaluation and get back with the price,” he said. “Some of them that we have done services for before, they just send us the scoop.”
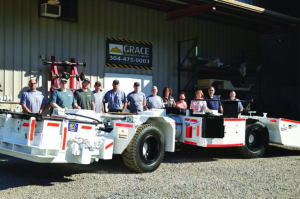
Grace Equipment Co. rebuilds almost any make and model scoop to its “original glory” and can upgrade it for improved clearance or rear end ratio. (Photo: Grace Equipment Co.)
Next, “we’ll tear it down to the frame, rebuild any parts of the frame, build new frames, put in the center sections, plumb it, wire it, put the lights on it, sandblast it, paint it, and then send it back to the customer.”
In other words, Grace Equipment rebuilds “it to its original glory,” the company said.
Sometimes customers want more than the original glory, and adopt modifications and upgrades. “Some people like to change the ratio on the rear ends on them,” Pearson said.
“Some people want a bit more ground clearance than others,” he said. “Some of them want to put on smaller tires. Some of them want to put on bigger tires, and we can make adjustments for that.”
Rebuilds offer several benefits.
“You are looking at a large sum of money to buy a brand new scoop when, for less, you can have one completely rebuilt and all the new updates put on it,” Pearson said.
Another benefit is the comparatively quick turnaround time.
“Some of your other rebuild shops, and I don’t knock any of them because I was in mining for 41 years and I used them all, but most of these shops are booked up and can’t get a rebuild out in time,” Pearson said.
“We’ve been fortunate,” he said. “We have a machine shop where we make the drive shafts and some of the component parts, and have
them in house.”
Grace Equipment can rebuild most makes and models. “We are fully equipped to handle any size mining scoop,” the company said.
“We do all the scoops that are out there,” Pearson said. “We get parts for them, and we make parts for them.”
The rebuild offering launched more than a decade ago.
Before that, Grace was “making the battery mantrips that haul the men underground and through the mines,” Pearson said. At the time, Pearson ran a contract mining operation at the Patriot mine, “and as Grace Equipment would build these new rides, they would bring them to me and we would try them out and work all the bugs out of them.”
The mantrips ultimately were sold “to Peabody Energy and some of the other larger companies out there,” he said.
Patriot folded amid a drop in coal prices. “So I went to work for Randy Workman, president of Grace Equipment, and helped him grow the business. We expanded into rebuild services and bought our warehouse and shop and its equipment,” Pearson said. “For the past 10 years we’ve done a wide variety of equipment rebuilds and component manufacturing.”
Over time, the offering grew, along with the demand for service. “We’ve proven that we can do the job,” Pearson said. “We stand behind our work.”
The company is staffed and equipped to go on location to support customers. “If we have to go underground, we go underground. We’ve got all our people certified for that,” Pearson said.
“Customer satisfaction is our top priority,” he said. “That is our number one goal.”